Why use ORFS Fittings?
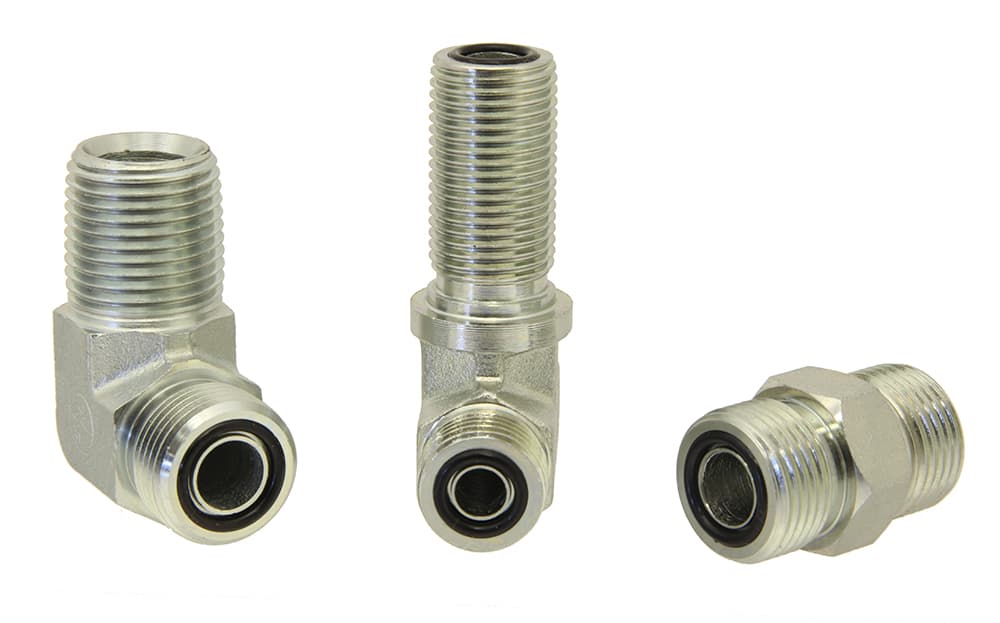
Image Description: An image of ORFS fittings on a white background
Thread Sizing
ORFS fittings come in straight threads with the outer diameter defined in-dash sizes and the pitch (the distance between each thread, measured in threads per inch or TPI) defined by the UTS (Unified Thread Standard). For example, a -9 –18 ORFS fitting has an outer diameter of 9/16” and 18 threads per inch. Each thread has an angle of 60O. Below are some common thread sizes used in the industry.

Note that the dash size is just multiplied by 1/16 to give the outer diameter in inches. The threads are defined by the Unified National Fine thread sizing, a subset of the UTS with a higher number of threads than the USC (Unified National Coarse) sizing specifications but lower than the UNEF (Unified National Extremely Fine) sizing specifications.
Advantages of Using ORFS Fittings
ORFS fittings have a list of advantages that are similar to ORB fittings. They, too, can withstand high pressure and vibrations on account of the mechanical seal offered by the o-ring. Additionally, it is easy to assemble and de-assemble them, with the o-ring being replaceable, allowing easy maintenance of fluid conveyance systems. Since they provide sealing at the mating surface, it reduces the chances of a leak occurring when a long thread fitting is used. This also means that damage to threads is highly unlikely as the o-ring compensates for variations due to tolerances.
ORFS fittings are ideal for use in gas delivery systems on account of the seal they provide and the normally low-temperature conditions associated with them.
The fittings themselves are widely available, coming in different sizes, materials like carbon and stainless steel, and product variations like tee, elbows, unions, and swivels.
Disadvantages of Using ORFS Fittings
Like ORB fittings, they too are limited by performance when it comes to withstanding temperature ranges. The o-ring can melt or erode if the temperature is too high or if the medium is incompatible. A phenomenon one needs to look out for is o-ring fallout, especially when it happens during assembly. The o-ring may fall out of its groove leading to an improper seal, the o-ring pinching outside of the intended surfaces, and thread damage due to overtightening. In this case, the o-ring and ORFS fitting may sustain damage beyond repair, making it completely unusable. Hence caution must be taken to ensure that the o-ring sits properly before assembly. Using an adhesive material during assembly may help overcome this issue.