Hydraulics vs Pneumatics: The Key Differences
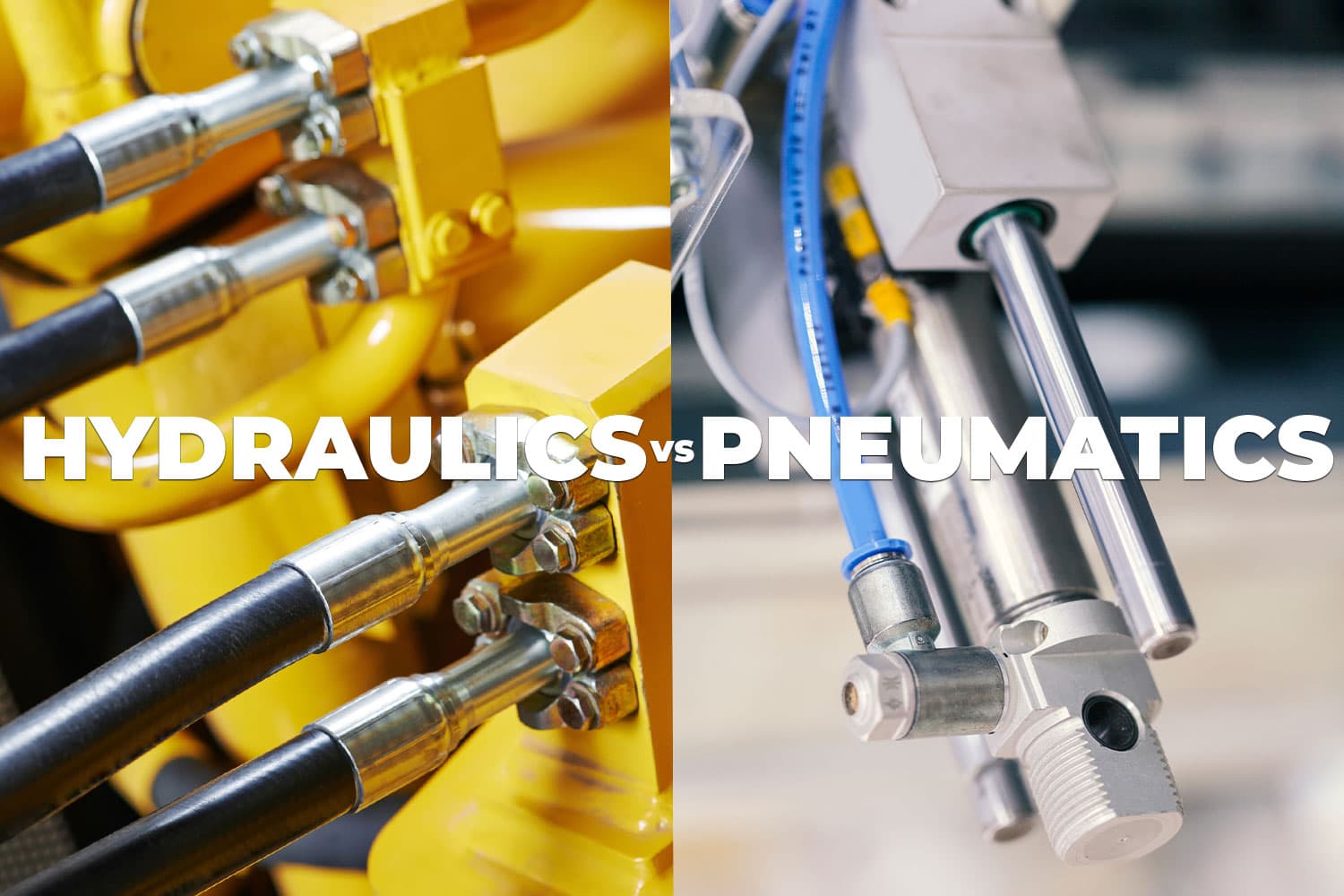
Hydraulics vs Pneumatics
When it comes to powering industrial machinery and equipment, two fundamental technologies stand out: hydraulics and pneumatics. Both systems are integral to numerous industries, from aerospace and manufacturing to agriculture and transportation. However, understanding the differences between these two technologies is crucial for selecting the right system for your specific application. In this blog, we will provide an expert overview of the key differences between hydraulics and pneumatics, examining their power and performance, efficiency and control, maintenance and durability, cost considerations, and safety and environmental impacts.
Power and Performance
Hydraulics: Hydraulics systems use liquids, typically oil, to transmit power. Due to the incompressibility of liquids, hydraulics can handle heavy loads and provide precise control over force and movement. This makes hydraulics ideal for applications requiring significant power, such as in aerospace, military, construction, and heavy manufacturing.
Pneumatics: Pneumatics systems use compressed air or other gases to transmit power. Air is compressible, which means pneumatic systems are generally less powerful than hydraulic systems but are faster and cleaner. Pneumatics is often used in applications requiring rapid movement and lighter loads, such as in food and beverage, packaging, and automation industries.
Efficiency and Control
Hydraulics: One of the standout features of hydraulic systems is their high efficiency and precise control. The ability to control the speed, position, and force with great accuracy makes hydraulics suitable for tasks where precision is critical. This includes applications in scientific research, energy, and power generation, where exact control can impact overall performance and safety.
Pneumatics: While pneumatic systems may not offer the same level of precision as hydraulics, they excel in simplicity and ease of use. Pneumatics provide sufficient control for many applications, especially those where high speed and frequency of operation are more important than precision. Their efficiency is notable in systems where continuous operation and low maintenance are key.
Maintenance and Durability
Hydraulics: Hydraulic systems generally require more maintenance due to the complexity of components and the need to manage fluid quality and contamination. However, they offer robust durability and longevity, making them suitable for harsh and demanding environments, such as in agriculture, construction, and transportation.
Pneumatics: Pneumatic systems are typically easier to maintain, with fewer components and lower risk of leaks. The use of air as a medium means that there are fewer issues related to fluid contamination. This makes pneumatics a go-to choice in industries where cleanliness is paramount, such as food and beverage, and where system downtime needs to be minimized.
Cost Considerations
Hydraulics: Initial setup costs for hydraulic systems can be higher due to the need for pumps, motors, and fluid reservoirs. However, their ability to handle large loads and provide precise control can result in cost savings over time through increased efficiency and reduced operational costs.
Pneumatics: Pneumatic systems often have lower initial costs and are generally more cost-effective for applications involving lighter loads and high-speed operations. The lower maintenance costs and ease of installation also contribute to their cost efficiency, making them a viable option for many industrial applications.
Safety and Environment
Hydraulics: While hydraulic systems are powerful, they require careful management to prevent leaks and spills, which can be hazardous and environmentally damaging. Proper design and maintenance are crucial to ensure safe operation in sectors like aerospace, military, and energy.
Pneumatics: Pneumatic systems are inherently safer in many respects because they use air, which poses no contamination risk in case of a leak. This makes them particularly suitable for applications in clean environments and those with stringent safety requirements, such as scientific research and food processing.
Conclusion
Choosing between hydraulics and pneumatics depends on the specific needs of your application. Hydraulics offer unmatched power and precision, making them indispensable for heavy-duty and high-stakes operations. Pneumatics, on the other hand, provide speed, simplicity, and cost-effectiveness, ideal for applications where rapid motion and cleanliness are critical.